Na czym polega wytłaczanie tworzyw sztucznych: kompletny przewodnik po procesie
Tworzywa sztuczne można spotkać wszędzie ze względu na wszechstronność ich zastosowania, trwałość i nieskomplikowane wymagania produkcyjne.
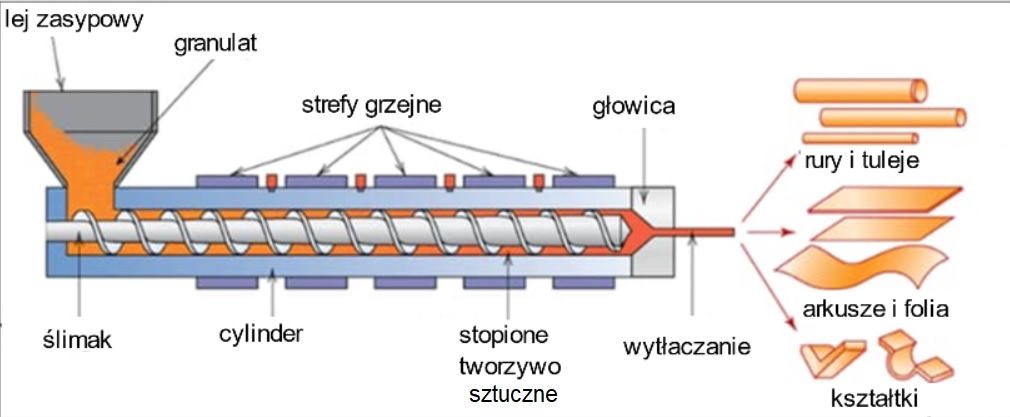
Wytłaczanie tworzyw sztucznych, wraz z formowaniem wtryskowym, jest jednym z najczęstszych procesów produkcji masowej. Ogólnie rzecz biorąc, wytłaczanie jest powszechnie stosowane w przypadku produkcji profili ciągłych takich jak rury, tuleje, profile drzwiowe i inne elementy gabarytowe.
Przemysłowe stosowanie wytłaczania tworzyw sztucznych miało swój początek ponad sto lat temu i rozwijało się w miarę upływu czasu. Nawet dzisiaj jest to sprawdzona metoda stosowana w wielu projektach związanych z produkcją tworzyw sztucznych, ponieważ jest prosta, wydajna i daje precyzyjne wyniki.
W poniższym artykule przyjrzymy się podstawom procesu wytłaczania tworzyw sztucznych. Poznamy jego zalety, ograniczenia, rodzaje i wreszcie wspólne zastosowania w różnych branżach przemysłowych.
Ogólny zarys procesu wytłaczania tworzyw sztucznych
Wytłaczanie tworzyw sztucznych to proces, w którym tworzywo sztuczne w postaci granulatu przechodzi przez różne elementy wytłaczarki, aby na końcu, dzięki zastosowaniu odpowiedniej temperatury i ciśnienia, uzyskać postać ciągłego profilu. Aby lepiej zrozumieć ten proces, należy najpierw dowiedzieć się czym jest wytłaczarka i poznać sposób jej działania.
Powyższe zdjęcie przedstawia zwykłą wytłaczarkę do tworzyw sztucznych, która składa się z następujących elementów:
Lej zasypowy: jest to pierwszy element wytłaczarki do tworzyw sztucznych. Jest on wypełniony tworzywem sztucznym w postaci granulatu, który jest wykorzystywany w dalszych etapach procesu produkcyjnego.
Podajnik: kieruje tworzywo sztuczne z leja zasypowego do cylindra wytłaczarki.
Płyta sitowa: ten element działa jak filtr cylindra i pomaga utrzymać ciśnienie.
Cylinder: jest to podgrzewany zbiornik wytłaczarki, w którym następuje zmiękczanie tworzywa sztucznego pod wpływem temperatury zbliżonej do temperatury topnienia materiału. Obracający się w cylindrze ślimak wtłacza materiał do rury zasilającej.
Rura zasilająca: działa jak element transportowy stopionego plastiku wychodzącego z cylindra.
Głowica: jest to sztywna metalowa część, przez którą przeciska się surowiec w celu wytłoczenia pożądanego profilu.
System chłodzenia: ostatni etap, w którym profil wytłaczany krzepnie na skutek szybkiego chłodzenia.
Na czym polega proces wytłaczania tworzyw sztucznych?
Proces wytłaczania tworzyw sztucznych rozpoczyna się od wypełnienia leja zasypowego małymi kawałkami plastiku, które są prostsze w obróbce. Podajnik, wykorzystując zjawisko grawitacji transportuje tworzywo sztuczne do cylindra, gdzie będzie ono poddane dalszemu przetwarzaniu.
Kiedy surowiec wchodzi do cylindra, zaczyna się nagrzewać na skutek oddziaływania co najmniej trzech stref grzewczych, w których następuje wzrost temperatury w miarę oddalania się surowca od podajnika.
Wraz ze wzrostem temperatury, ślimak stale obracający się w cylindrze popycha stopione tworzywo sztuczne w kierunku następnego elementu maszyny. Ślimak i ciśnienie powstające na skutek przepychania surowca w cylindrze powodują wytwarzanie się dodatkowego ciepła, dlatego też temperatura stref grzewczych nie musi być tak wysoka, jak oczekiwana temperatura wytłaczania. To pozwala oszczędzić energię i ułatwia proces wytłaczania.
Płynne tworzywo sztuczne opuszcza cylinder przez siatkę zamocowaną na płycie sita. To sito pozwala wyeliminować obce substancje z surowca i utrzymuje ciśnienie wewnętrzne. Surowiec przechodzi przez rurę zasilającą do specjalnie wykonanej głowicy, która ma taki sam kształt jak profil, który będzie wytłoczony zgodnie z projektem.
Opór, jaki stawia głowica przesuwanemu przez ślimak stopionemu tworzywu, sprawia, że surowiec przechodząc przez głowicę, przybiera taki sam kształt jak jej otwór, co kończy proces wytłaczania.
Po całkowitym przejściu przez głowicę wytłoczony profil jest chłodzony prysznicem wodnym lub za pomocą zestawu rolek chłodzących, co zapewnia utrwalenie kształtu wytłoczonego termoplastycznego profilu.
Wytłaczanie tworzyw sztucznych na przestrzeni historii
Wytłaczanie zawsze wiązało się z wytwarzaniem produktów na dużą skalę. Wszystko zaczęło się w Niemczech, kiedy Paul Troester stworzył pierwszą wytłaczarkę do plastiku. Od tego czasu podstawowy przebieg procesu niewiele się zmienił.
Jednakże wprowadzono wiele ulepszeń w procesie wytłaczania w odniesieniu do jego wydajności i możliwości obsługi surowca. W przeszłości urządzenia do wytłaczania mogły przetwarzać tylko określone rodzaje tworzyw sztucznych i miały wiele wymagań. Z czasem sytuacja zmieniła się na lepsze, i dzisiaj wytłaczanie tworzyw sztucznych ma charakter bardziej wszechstronny, elastyczny i umożliwia przetwarzanie różnych rodzajów tworzyw sztucznych jednocześnie.
Innym częstym problemem związanym z wytłaczaniem tworzyw sztucznych jest fakt, że nie posiadają one odpowiednich właściwości mechanicznych i wytrzymałościowych. W przeszłości stanowiło to poważny problem, ale nowe osiągnięcia technologiczne poprawiły sytuację. Obecnie preferowanym procesem jest wytłaczanie tworzyw sztucznych na zamówienie, ponieważ zapewnia ono jakość, spójność i funkcjonalność oczekiwaną od nowoczesnych zastosowań przemysłowych.
Różne rodzaje procesów wytłaczania tworzyw sztucznych
Rodzaj procesu wytłaczania zależy od kształtu głowicy. Chociaż podstawowy proces wytłaczania tworzyw sztucznych pozostaje taki sam, różne rodzaje procesów pozwalają skutecznie radzić sobie ze złożonością i zawiłościami wynikającymi z produkcji artykułów o różnych kształtach.
Oto 4 główne rodzaje procesów wytłaczania tworzyw sztucznych obecnie stosowanych w przemyśle.
1 – Wytłaczanie rur
Proces ten dotyczy długich przewodów rurowych, rur i innych podobnych produktów. Ogólnie rzecz biorąc, wytwarzanie produktu pustego w środku jest trudniejszą kwestią. Pomimo tego, ten proces wytłaczania pozostaje taki sam, do momentu dotarcia surowca do głowicy. Na tym etapie, w procesie wytłaczania wykorzystuje się dodatnie ciśnienie wewnętrzne, uzupełniając w ten sposób wyższe wymagania związane z poborem mocy podczas przetwarzania elementów pustych w środku.

2 – Wytłaczanie folii z rozdmuchem
Proces wytłaczania folii z rozdmuchiwaniem jest dość powszechnie stosowany, ponieważ pozwala wyprodukować wiele przedmiotów codziennego użytku, takich jak torby na zakupy i inne materiały opakowaniowe. Ten proces nie różni się od innych rodzajów wytłaczania (na przykład od wytłaczania aluminium). Jednakże istnieje podstawowa różnica polegająca na tym, że w tym procesie wytłaczania, zanim surowiec opuści głowicę, zostaje schłodzony.

Na tym etapie materiał nie twardnieje całkowicie. Dlatego później przechodzi dodatkowy proces rozprężania poprzez rozdmuch. Proces ten jest stosowany tylko do produkcji cieńszych folii z tworzyw sztucznych. W przypadku grubszych folii konieczne jest zastosowanie innego procesu wytłaczania.
3 – Wytłaczanie folii płaskiej
Proces ten jest bardzo podobny do wspomnianego wcześniej wytłaczania folii z rozdmuchiwaniem. Jest on jednak stosowany w przypadku wytwarzania produktów zbyt grubych, aby możliwe było przetwarzanie ich metodą rozdmuchu. W tym przypadku materiał przechodzi przez proces ciągnięcia i walcowania, który nadaje mu pożądany kształt.

Podczas procesu walcowania tworzywo sztuczne zostaje jednocześnie schłodzone, co umożliwia jego trwałe zestalenie. Ogólnie rzecz biorąc, proces ten pozwala wytworzyć w łatwy sposób pudełka na lody, kartony do soków, pudełka na wino i inne grubsze plastikowe opakowania.
4 – Powlekanie
Następny rodzaj wytłaczania dotyczy przewodów izolacyjnych i innych podobnych zastosowań, w których dany element jest pokrywany całkowicie tworzywem sztucznym. Sam proces nie jest skomplikowany. Dany materiał, który wymaga powleczenia, jest przeciągany przez głowicę, tak aby nałożyć na niego plastikową osłonę.

W zależności od wymagań i zastosowania końcowego produktu może zaistnieć również konieczność zapewnienia przyczepności pomiędzy tworzywem sztucznym a powlekanym materiałem. W takim przypadku wystarczy użyć oprzyrządowania wykorzystującego ciśnienie. Dzięki takiemu prostemu rozwiązaniu, na materiał powlekający zostaje wywarte wystarczające ciśnienie, co zapewnia doskonałą przyczepność utrzymującą się przez długi czas.
Rodzaje wytłaczarek do tworzyw sztucznych
Jeśli myślisz o zainwestowaniu w wytłaczarkę do tworzyw sztucznych, będziesz mieć możliwość wyboru wytłaczarki jednoślimakowej lub dwuślimakowej. Oba urządzenia umożliwiają przeprowadzenie wszystkich omówionych wcześniej procesów. Jednakże, zastosowanie danego typu wytłaczarki może wpływać na szybkość produkcji, możliwości mieszania surowca i ogólną elastyczność procesu.
A oto bardziej szczegółowe informacje odnośnie możliwości oferowanych przez każdą z ww. wytłaczarek.
Wytłaczarka jednoślimakowa
Jak sama nazwa wskazuje, wytłaczarki jednoślimakowe to proste urządzenia z jednym ślimakiem obracającym się wewnątrz cylindra. Ogólnie rzecz biorąc, wytłaczarki jednoślimakowe są idealnym rozwiązaniem w przypadku wytłaczania prostych profili, takich jak rury, oraz w produkcji folii. Mimo to, że wytłaczarki jednoślimakowe sprawują się całkiem dobrze, są one nieco wolne, nie mieszają surowca zbyt dokładnie i mogą nie stanowić najlepszego wyboru w przypadku wytłaczania skomplikowanych kształtów.

Wytłaczarki dwuślimakowe
Jak sama nazwa wskazuje, wytłaczarki dwuślimakowe mają dwa równoległe ślimaki w cylindrze. W zależności od zastosowanego procesu produkcyjnego oba ślimaki mogą obracać się w tym samym kierunku lub w różnych kierunkach. Ze względu na swoją konstrukcję, wytłaczarki dwuślimakowe zapewniają większą stabilność, skuteczniejsze odprowadzanie gazów, szybkość i wydajność mieszania.

Zalety wytłaczania tworzyw sztucznych
Wytłaczanie to popularna metoda produkcji seryjnej na dużą skalę, która stanowi idealne połączenie wszechstronności, elastyczności i spójności. Oto niektóre z głównych zalet procesu wytłaczania tworzyw sztucznych:
Opłacalność produkcji: w porównaniu z innymi procesami zastosowanie wytłaczania jest stosunkowo racjonalne pod względem kosztów. Ogólnie rzecz biorąc, artykuły z tworzyw sztucznych są wytwarzane albo poprzez formowanie wtryskowe, albo poprzez wytłaczanie. Jednakże wytłaczanie nie wymaga stosowania skomplikowanego oprzyrządowania i jest znacznie prostsze, co skutkuje niższymi kosztami. Co więcej, urządzenia do wytłaczania mogą również pracować w sposób ciągły, bez żadnych przerw, co zapewnia 24-godzinną produkcję zapewniającą odpowiedni poziom zapasów wytłaczanych produktów.
Niezrównana elastyczność: pod warunkiem zachowania spójności przekroju produktu, można uzyskać dowolny kształt lub profil w procesie wytłaczania tworzywa sztucznego. Proces wytłaczania pozwala uzyskać wiele przekrojów profili począwszy od bardziej skomplikowanych form po arkusze, rury i inne kształty.
Możliwość zmian: zanim rozpocznie się proces chłodzenia, gorące tworzywo sztuczne zachowuje stosunkowo plastyczną formę. Oznacza to, że mamy możliwość dokonania poprawek kształtu wytłaczanego profilu w łatwy sposób, tak aby wymiary końcowego produktu odpowiadały naszym wymaganiom.
Wypróbuj RapidDirect teraz!
Wszystkie informacje i przesłane pliki są bezpieczne i poufne.
Główne zastosowania wytłaczania tworzyw sztucznych
Ze względu na fakt, że jest to jedna z głównych metod wytwarzania części z tworzyw sztucznych, zastosowanie procesu wytłaczania jest bardzo szerokie. Poniżej przedstawiono niektóre z najważniejszych obszarów, w których integralną rolę odgrywają technologie wytłaczania tworzyw sztucznych.
Rury i tuleje
Rury i tuleje należą do najpopularniejszych produktów wytwarzanych w procesie wytłaczania tworzyw sztucznych. Wymagania odnośnie głowicy wytłaczarki są również niewielkie, ponieważ jedyną, niezbędną rzeczą jest prosty cylindryczny profil. Rury PVC są również niezwykle popularne w przemyśle, ale istnieją też inne alternatywy. Niezależnie od zastosowanego materiału istnieje duże prawdopodobieństwo, że rury i tuleje powstały w procesie wytłaczania tworzywa sztucznego.

Izolacja przewodów
Tworzywa sztuczne, ze swojej natury, wykazują doskonałe właściwości izolacji elektrycznej. Ponadto ich naturalna elastyczność i stabilność termiczna sprawiają, że są idealnym wyborem jeśli chodzi o izolację i osłonę przewodów pod napięciem. Na dobra sprawę, większość produktów stosowanych do osłony i izolacji przewodów powstaje w wyniku procesu wytłaczania, ponieważ jest on najłatwiejszy i zapewnia długotrwałe rezultaty.
Okna
Ramy okienne to kolejne powszechne zastosowanie wytłaczanych tworzyw sztucznych. Wiele osób używa do tego celu PVC, ze względu na jego trwałość i naturalną odporność na promieniowanie UV.
Drzwi
Podobnie jak okna, ościeżnice również należą d produktów powstających w wyniku procesu ekstruzji ze względu na możliwość uzyskiwania ciągłego profilu o stałym przekroju. PVC jako surowiec jest bardzo popularne, jeśli chodzi o ościeżnice i inne elementy wyposażenia domu ze względu na swoją stabilność i doskonałe właściwości mechaniczne.
Żaluzje i rolety
To kolejny klasyczny przykład tego, jak powszechny jest proces wytłaczania. W żaluzjach i roletach często występuje wiele identycznych rowków, które umożliwiają łączenie poszczególnych elementów zapewniających funkcjonalność tych produktów. Wytłoczone elementy z polistyrenu (popularne tworzywo sztuczne), mogą imitować wygląd drewna — zjawisko , z którym można się często spotkać przy produkcji zwykłych żaluzji.
Sprzęt do czyszczenia
Uchwyty wycieraczek, ściągaczek wody i innych artykułów do czyszczenia są wykonane z tworzywa sztucznego. W niektórych produktach znajdują się nawet elementy z gumopodobnego tworzywa sztucznego umożliwiające skuteczniejsze czyszczenie i dlatego, aby wytworzyć je w dużych ilościach, niezbędne jest zastosowanie procesu wytłaczania.
RapidDirect: najlepszy wybór w zakresie wysokiej jakości usług wytłaczania tworzyw sztucznych
Wytłaczanie tworzyw sztucznych stanowi częsty wybór ze względu na fakt, że jest to proces stosunkowo nieskomplikowany, opłacalny i dający się zastosować w wielu projektach. Nie oznacza to jednak, że jest to rozwiązane dla każdego. Zastosowanie technologii wytłaczania wymaga spełnienia wielu warunków wstępnych, wymagań stawianych przez sam projekt i innych istotnych kwestii, które pozwalają osiągnąć zadowalające wyniki. Co więcej, rozpoczęcie wytłaczania wymaga również zainwestowania w wiele urządzeń i odpowiednie oprzyrządowanie.
Dla małych i średnich firm inwestowanie tak dużej ilości czasu i zasobów jest niepraktyczne. W tym przypadku najlepszym wyborem jest kompleksowa i doświadczona usługa wytłaczania, jaką oferuje RapidDirect.
Firma RapidDirect stara się być czymś więcej niż zwykłym dostawcą usług. Jesteśmy punktem kompleksowej obsługi wszystkich potrzeb produkcyjnych klienta, począwszy od fazy projektowania po optymalizację. Posiadając najnowsze maszyny i najbardziej doświadczony zespół, jesteśmy w stanie zapewnić najlepsze połączenie jakości, niezawodności i wydajności w możliwie najkrótszym czasie.
Jedną z rzeczy wyróżniających firmę RapidDirect, jest kompleksowa platforma do wyceny online. Posiadamy najbardziej zaawansowany system, który umożliwia natychmiastową wycenę projektu.
Wystarczy wprowadzić dane projektu wraz z jego specyfikacją, a my przedstawimy wszystkie przewidywane koszty rozpoczęcia produkcji. Ponadto oferujemy również bezpłatny raport — Projektowanie produkcji (DFM), który pomoże zoptymalizować projekt i usprawnić cały proces umożliwiając w ten sposób uzyskanie najlepszych wyników.
Informacje dodatkowe: Porównanie wytłaczania plastiku i aluminium
Wytłaczanie nie ogranicza się jedynie do tworzyw sztucznych. Proces wytłaczania profilu ciągłego może być również zastosowany do produkcji części metalowych. Ogólnie rzecz biorąc, aluminium należy do metali najczęściej poddawanych procesowi wytłaczania ze względu na wytrzymałość materiału, gęstość, możliwość recyklingu i inne właściwości mechaniczne.
Dzisiaj wytłaczanie aluminium jest powszechnym procesem produkcyjnym, w ramach którego powstają produkty takie jak pręty, szyny, rury, radiatory i wiele innych elementów. W przypadku gdy rzeczą ważną jest, aby produkt miał postać profilu ciągłego o równomiernym przekroju poprzecznym, aluminium spełnia te wymagania.
Ponadto istotną różnicą między procesem wytłaczania tworzyw sztucznych a wytłaczaniem aluminium jest temperatura.
W przeciwieństwie do tworzyw sztucznych wytłaczanie aluminium może odbywać się zarówno "na gorąco" jak i "na zimno". Wytłaczanie "na zimno" pozwala uzyskać produkty o wysokiej wytrzymałości, ale wymaga zastosowania większej siły. Z drugiej strony, wytłaczanie "na gorąco" odbywa się w temperaturze od 350°C do 500°C, co ułatwia proces, jednakże odbywa się kosztem właściwości mechanicznych produktu.
Dział: Inżynieria Materiałowa
Autor:
Rapid Direct | Tłumaczenie: Piotr Kolarzyk
Źródło:
https://www.rapiddirect.com/blog/plastic-extrusion-process/